Курсовая работа: Оптимізація технологічних процесів в гнучких виробничих системах
3)
Т1 Т2 Т3 Ф1 Ф2 Т4 Т5
4)
Т1 С1 Т2 Т3 Ф1 Ф2 Т5
5)
Т1 С1 С2 Т3 Ф1 Ф2 Т4
6)
Т1 С1 Т3 Ф1 Ф2 Ф3 Р2
7)
Т2 Т3 Ф1 Ф2
Тут буква – позначення типу операції, цифра – номер операції.
Розбиття
процесів на групи:
Знаходиться
найбільше число операцій для всіх об’єктів:
Р=11=Т2+С2+Т3+Ф1+Ф2+Т4+Ф3+Р2+Т1+Т5+С1
Будується
квадратична матриця, вона заповнюється по формулі
aij=Р-Рj
де Pj – кількість різних операцій, між порівнюваними об’єктами.
а12=11-5=6
а23=11-5=6 а34=11-2=9 а45=11-4=7 а56=11-4=7
а67=11-5=6
а13=11-4=7
а24=11-7=4 а35=11-4=7 а46=11-4=7 а57=11-5=6
а14=11-4=7
а25=11-5=6 а36=11-6=5 а47=11-3=8
а15=11-4=7
а26=11-3=8 а37=11-3=8
а16=11-6=5
а27=11-4=7
а17=11-1=10
В
матриці береться максимальне число, записуються його координати, потім
знаходиться таке саме число і записується змінена координата. Так утворюється
технологічна група. Потім береться наступне максимальне число і операції
повторюються до тої пори, поки в групах не будуть всі об’єкти. В нову групу не
беруться числа, які є в попередніх групах.
І=[1, 7]
ІІ=[3, 4]
III=[2, 6]
IV=[5]
Таким
чином, утворилися чотири технологічні групи, які містять у собі всі об’єкти.
Аналіз:
Технологічні
групи представляються, як комбінації операцій, які виконуються, над їх об’єктами.
Проводиться спроба об’єднати технологічні групи по сукупності спільних
операцій:
І=Т2
С2 Т3 Ф1 Ф2
ІІ=Т1
Т2 Т3 Ф1 Ф2 Т4 Т5 С1
ІІІ=Т3
Ф1 Ф2 Т4 Ф3 Р2 Т1 С1
IV=Т1 С1 С2 Т3 Ф1 Ф2 Т4
В
нашому випадку об’єднання здійснити неможливо. Тому у нас залишаються усі
чотири групи.
Закріплення операцій за модулями
Для
розробки групового технологічного процесу необхідно визначити кількість ГВМ,
які входять у ГВС і вибрати основне технологічне обладнання. Основне ТО
необхідно вибрати з однієї сторони – на основі структурно-технологічної схеми
процесу обробки, з іншої – з урахуванням конкретної автоматизованої
транспортно-складської системи. Процес вибору ТО передбачає розподілення
технологічних операції по ГВМ.
Для
визначення числа ГВМ використовується метод графів. Структурно-технологічні
схеми представлені у вигляді графів (рис. 1.1, 1.2, 1.3, 1.4), вершини яких –
групові операції, дуги послідовність виконання операцій.
Побудова
графів:
Отримані
групи розкладаються на вихідні деталеоперації, по яких будується граф.
І=Т2
С2 Т3 Ф1 Ф2
1)
Т2 С2 Т3 Ф1 Ф2
7)
Т2 Т3 Ф1 Ф2
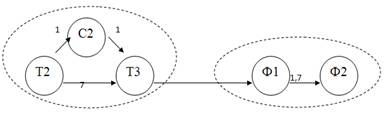
рис.1.1
ІІ=Т1
Т2 Т3 Ф1 Ф2 Т4 Т5 С1
3)
Т1 Т2 Т3 Ф1 Ф2 Т4 Т5
4)
Т1 С1 Т2 Т3 Ф1 Ф2 Т5
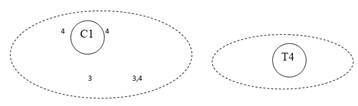
Рис
ІІІ=Т3
Ф1 Ф2 Т4 Ф3 Р2 Т1 С1
2)
Т3 Ф1 Ф2 Т4 Ф3 Р2
6)
Т1 С1 Т3 Ф1 Ф2 Ф3 Р2
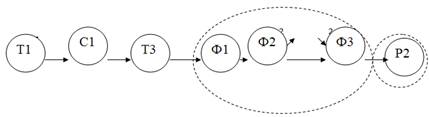
Рис.1.3
IV=Т1 С1 С2 Т3 Ф1 Ф2 Т4
5)
Т1 С1 С2 Т3 Ф1 Ф2 Т4
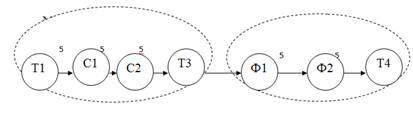
Рис.1.4
Пунктиром
позначено об’єднання операцій у технологічні модулі.
Для
визначення числа ГВМ, потрібно зобразити графи рис.1.1, 1.2, 1.3, 1.4 у вигляді
модулів і оптимізувати їх.
І:
Т1
С2 Т3 Ф1 Ф2
1,7
IV:
Т1 С1 С2 Т3 Ф1 Ф2 Т4
5
Рс.1.8
Далі
проводиться об’єднання і оптимізація технологічних модулів.
М2=[Ф1 Ф2]
М1/=[Т1 С1 Т2 Т3]
М2/=[Ф1 Ф2 Т4 Т5]
М1//=[Т1 С1 Т3]
М2//=[Ф1 Ф2 Т4 Ф3]
М3//=[Р2]
М1///=[Т1 С1 С2 Т3]
М2///=[Ф1 Ф2 Т4]
Для
цього знищується дубль операції в модулях.
Отримаємо:
М1=[Т2 С2 Т3]
М2=[Ф1 Ф2]
М1/=[Т1 С1]=М3
М2/=[Т4 Т5]=М4
М2//=[Ф3]=М5
М3//=[Р2]=М6
Взаємодія
технологічних модулів має наступний вигляд:
Як
видно з графу (рис.1.10), це об’єднання дало позитивний результат – система
стала лінійною:
Т1
С1 Т2 С2 Т3 Ф1 Ф2 Т4 Т5 Ф3 Р2
 3,4,5,6 1,2,3,4,5,6,7
Рис.1.10
Таким
чином число ГВМ, які потрібні для реалізації ГВС – 3.
Структурно-технологічна
схема (розбивка ГВС на ГВМ):
На
структурно-технологічній схемі вказано входи у ГВМ деталей, переходи деталей
між ГВМ та виходи деталей з модулів.
система
стала лінійною:
Т1
С1 Т2 С2 Т3 Ф1 Ф2 Т4 Т5 Ф3 Р2
3,4,5,6
1,2,3,4,5,6,7 1,2,3,4,5,6,7
2. Розрахунок складу устаткування для транспортування деталей
Склад
устаткування для транспортування об’єктів виробництва включає: стелаж для
нагромадження, позиції завантаження і розвантаження, позиції контролю й
автономний транспортний модуль.
2.1 Визначення характеристик АС
Місткість
автоматизованого складу (АС) є основною його характеристикою. Вона визначається
числом носіїв, необхідних для повного завантаження ТУ під час роботи ГВС.
Це
число в свою чергу можна визначити максимальним числом деталеустановок, що
можуть бути оброблені ГВС, а оскільки ГВС випускає деталі різної номенклатури,
то доцільно мати 10%-ий запас чарунок на випадок збільшення обсягу продукції.

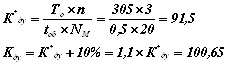
де n- число ГВМ. Отримане число
деталеустановок відповідає числу чарунок у стелажі – 101 чарунки.
2.2 Розрахунок числа позицій завантаження / розвантаження
Є
два види позицій завантаження і розвантаження – це роз’єднані і об’єднані. При
поділі функцій розвантаження і завантаження повинні бути два робочих місця, а
при об’єднанні – одне. Якщо воно встигає за часом виконувати весь необхідний
обсяг робіт. Розрахунок числа позицій здійснюється по формулі:
 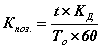
де t – трудомісткість операцій
з/р чи сполучених операцій. При розділених операціях у ГВС повинно бути 2
робочих місця, а при об’єднаних – 1 робоче місце, якщо воно устигає виконувати
обидві операції; КД –число деталеустановок, що проходять через 1 ГВМ
в один місяць:
(чарунок)
Для
вибору виду позицій
-
Кількість позицій
завантаження:
 (шт)
-
Кількість позицій розвантаження:
 (шт)
Загальне
число позицій завантаження / розвантаження:
 (шт)
2.
Використовуючи сполучені
позиції завантаження / розвантаження
Трудомісткість
сполучених операцій завантаження і розвантаження буде наступною:
 (хв)
Кількість
позицій завантаження / розвантаження:
 (шт)
Як
бачимо, при чистому розрахунку розділених позицій завантаження і розвантаження,
їх загальна завантаженість майже дорівнює 1, але оскільки варіант з суміщеними
позиціями з/р є економічно вигіднішим, та враховуючи те, що при розділених
позиціях завантаження і розвантаження, при виході зі строю однієї з позицій,
ГВС перестане функціонувати, оберемо варіант з суміщеними з/р.
2.3 Розрахунок числа позицій контролю
Якщо
об’єкти виробництва обробляються на декількох ГВМ, то контроль проводиться
після обробки на кожній з них.
Розрахунок
числа позицій контролю здійснюється по формулі:
 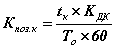
де tк – сумарний час контролю однієї ДУ
Він
визначається по формулі:

де r – середня кількість
операцій, що приходиться на один об’єкт (сума операцій по всіх об’єктах,
поділена на кількість деталей )
(дет)
Тоді
(хв)
КДК – число
деталеустановок, що проходять на контроль за місяць:
,
де ,
а1 і а2
- поправочні коефіцієнти, що враховують 1 ДУ і вивід на контроль у
зв’язку з використанням нового інструмента.
а1=1,15
а2=1,05
Тоді
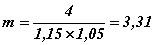
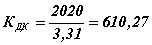
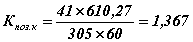
Для
того, щоб позиції контролю устигали виконувати весь необхідний обсяг роботи,
треба обчислену кількість прийняти рівною більш цілому числу, тобто у даному
випадку це буде число 2.
Отже,
для того, щоб ГВС працювала продуктивно необхідно мати 2 позиції позиції
контролю.
Необхідно
розрахувати середню кількість модулів, що приходяться на один об’єкт. Для цього
спочатку потрібно розписати кожен об’єкт через модулі, що він проходить:
1)
М1 М2
2)
М1 М2
3)
М3 М1 М2
4)
М3 М1 М2
5)
М3 М1 М2
6)
М3 М1 М2
7)
М1 М2
Розділимо
сумарну кількість модулів, через які проходять об’єкти, на кількість об’єктів і
округлимо отриманий результат. Тоді середня кількість модулів, що приходиться
на один об’єкт, буде рівна:
(2+2+3+3+3+3+2)/7=18/7=2,57
Отже,
середня кількість модулів, що приходиться на один об’єкт, рівна 3.
Граф
переміщень (рис. 2.4.1) дає нам число переміщень між ГВМ, складами і позиціями.
Знаючи відстань між ГВМ і швидкість переміщення АТМ, можемо розрахувати час обслуговування
АТМ із боку ГВМ.
Граф
переміщень
К2=3030
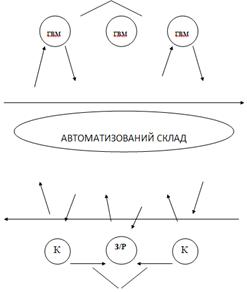
Рис
К4=505
Сумарний
час роботи АТМ:
(год)
Розрахувавши
сумарний час обслуговування ГВМ, можна розрахувати число необхідних АТМ для
виконання даної роботи через коефіцієнт завантаження:
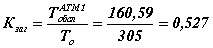
Отже,
для виконання всієї роботи з обслуговування ГВМ нам потрібно взяти 1 АТМ.
2.4 Розрахунок числа АТМ із боку позицій завантаження /
розвантаження
АТМ
із боку позицій завантаження / розвантаження служать для подачі порожніх
супутників на позицію завантаження, подачі завантажених супутників на склад та
доставки на позиції контролю і розвантаження.
Обчислимо
час обслуговування АТМ із боку позицій завантаження / розвантаження і контролю:
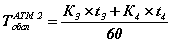
де К3
– число переміщень між АС і позиціями,
К4
– число переміщень між позиціями,
t3 – час передачі супутника зі стелажа на позицію,
t4
– час передачі супутника з позиції на
позицію.
К3=505+757+2020+1515+505+757=6060;
К4=252*2=505
t3=t4=tпер=1,06 (хв)
(год)
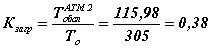
По
цьому коефіцієнтові завантаженості визначаємо число АТМ із боку позицій
3.Визначення складу устаткування для транспортування інструментів
3.1 Розрахунок складу інструментів
Основною
характеристикою складу інструментів є його місткість, що визначається числом
інструментів, необхідних для обробки всієї номенклатури деталей. Таке число
інструментів визначається по формулі:

де К1
– це число інструментів для обробки всієї номенклатури деталей, яке
визначається по формулі: , причому
Кду в цій формулі береться без обліку 10% запасу, tін – середній час роботи одного інструмента, а , де nдуб – число дублерів інструментів для обробки місячної програми.
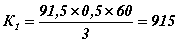

Тоді
(шт)
3.2 Визначення роботів-автооператорів
У
даному випадку будемо використовувати систему транспортування інструментів з
центральним багатомірним складом, розташованим над ГВМ. Така система вимагає
наявності транспортних пристроїв, для доставки інструментів до ГВМ і виводу
його із системи.
Виходячи
із місткості магазинів ГВМ і з місткості одного ряду інструментів у складі,
визначаємо кількість рядів інструментів у багатомірному АСІ.
Якщо
склад інструментів складається більш ніж з двох рядів інструментів, то для
організації введення і виводу інструментів у склад використовується
піднімальний пристрій. необхідна продуктивність піднімального пристрою
визначається по формулі:
,
де m – коефіцієнт, що враховує
партіонність деталей:
m=3,5 – якщо 50 % деталей виготовляються півмісячними партіями;
Тny – місячний фонд роботи
піднімального пристрою, він дорівнює То.
Тоді
необхідна продуктивність
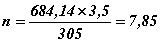
3.2.1 Визначення числа Р/А з боку ГВМ
Роботи-автооператори
здійснюють доставку інструментів у магазини ГВМ і назад. Для визначення їх
числа потрібно знати час однієї зміни інструмента і число змін інструментів в
місяць.
Сумарний
час, затрачуваний на обслуговування ГВМ, визначається по формулі:
,
де Ксм
– число змін інструментів на одному ГВМ протягом місяця.
,
де - число додаткових змін
інструмента на одному ГВМ, зв’язана з некомплектністю інструмента.
nду – число
деталеустановок, одночасно оброблюваних на ГВМ,
nін – число інструментів, що не розміщаються в магазині ГВМ. За умовою,
це 2 інструмент на 3 ДУ, тому nін =2/3.
Тоді


tcм – час зміни одного
інструмента

де (хв) – час на
підхід до чарунки складу й узяття інструмента,
(хв) – час на підхід до магазина інструментів і узяття
інструмента,
(хв) – час на поворот і установку
За
коефіцієнтом завантаженості одержуємо
число роботів-автооператорів з боку ГВМ – 1 шт.
3.2.2 Розрахунок числа Р/А, розташованих усередині автоматизованого
складу інструментів
Роботи-автооператори,
які розміщуються всередині автоматизованого складу інструментів виконують
функції введення і виведення інструментів, а також обмін інструментами між
лініями складу. Для визначення необхідного числа Р/А необхідно визначити число
переміщень Р/А в цій зоні і час одного переміщення.
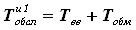
Твв
– час вводу/виводу інструментів із ГВС у годинах

(шт) – число
інструментів, що підлягають введенню та виведенню із системи протягом місяця;
- час одного вводу/виводу.
(хв) – підійти до касети і взяти з неї інструмент,
(хв) – час на підхід до гнізда з кодовим пристроєм і
установку інструмента, де tоп.н – час
визначення номера інструмента, залежить від використовуваного програмного
забезпечення і приблизно становить 0,1 хв,
Страницы: 1, 2, 3
|